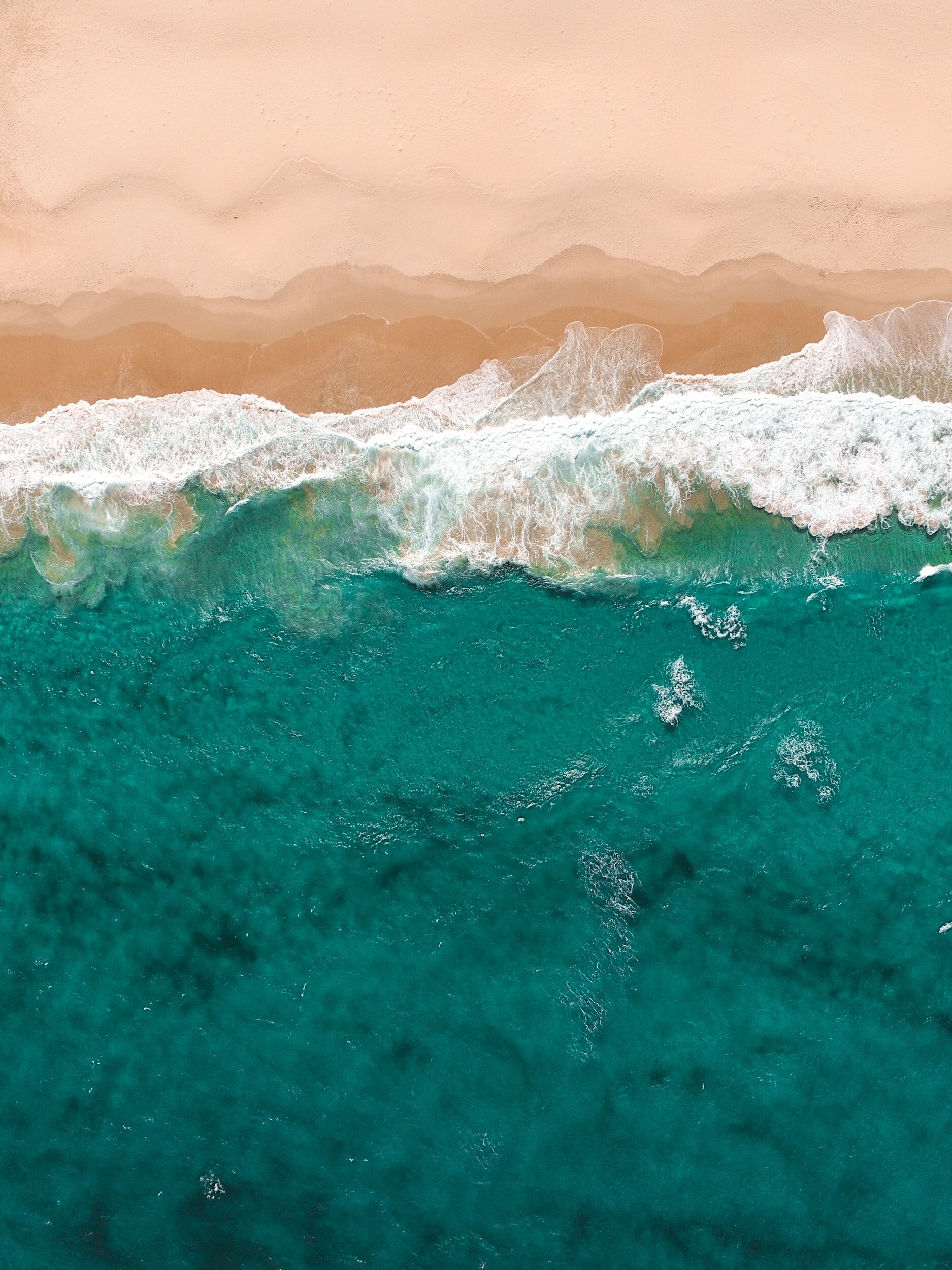
January 2023 - Current
ReefRanger
Conceptualisation
ReefRanger started off as an idea I created earlier in my sophmore year at UCLA. As a diver who had grown up seeing the damage happening to our world’s reefs, I wanted to use the engineering skills I had learned through other projects and clubs at UCLA to make a meaningful impact. It started off with conversations with professors at UCLA about creating a product that could autonomously plant artificial reefs. One of the things that drew me to furthering this idea was my own experiences as a diver who helped with creating artificial reefs. I understood how expensive and time consuming the process of implementing artificial reefs were. First, you needed volunteer divers who are willing to help out, secondly, you require dive supplies which can become costly, and lastly, you can only plant a couple of artificial reefs during each dive. Therefore, I was drawn to the idea of creating a product that could help autonomize this process, and aid divers in creating artificial reefs.
Following from this initial idea came months of brainsntorming with 2 friends I brought onto this project. We iterated through designs of creating fully working ROVs with hard grippers to be coral planters, to creating our own form of an artificial reef following tree artificial reef designs alongside potential collapsing mechanisms. Some of these brainstormed ideas can be seen below
Finally, we settled our final idea that employed the use of a soft robotic actuator. We decided our final vision would be to create a coral planter- our ReefRanger- which would be an ROV connected to this soft robotic actuator to delicately handle coral and plant them by working with other artificial reef companies, and by employing potential outplanting methods.
Towards the end of my sophmore year, I reached out to Professor Jawed, who is in charge of UCLA’s Structures and Computer Interaction Lab, who saw potential in our idea, and decided to take on our project under his lab. Currently, we are a team of 4, guided by a grad student, focused on bringing our design to life.
Our Soft Actuator
Our current focus in the lab is creating a working model of our soft robotic actuator. Our design is inspired by the process of peristalsis seen by organism's esophagus. The motivation behind using a soft actuator to handle coral comes from 2 main reasons 1) Coral are gentle organisms which require soft and minimially invasive handling and 2) Soft robotic actuators can mold to the shape of whatever it is handling. Furthermore, soft robotic actuators tend to be controlled primarily through pnematics, and potentially hydraulics, which are much more suitable for underwater uses over using fully electrical components.
One of the main components of our research involves figuring out how we can use strain limiting materials to change the strains across channels in our actuator to better mimic an esophagus. It also involves looking at the viability of using hydraulics over pnematics, as one vision we have for this actuator is for it to be controlled by recycled sea water.
Our actuator is primarily composed of silicone, and molded using 3D printed molds, a demolding agent, and our silicone material known as ecoflex. Currently, we are iterating through different potential designs, whos ideas can be seen below:
Design 1
Our first design was probably our most complex one to date. Unsure about how to create this fully working mechanism, we initially designed a mold that would let us create channels for air to be contained in, that we then planned to wrap around (we would have 2 of these molds for both sides. We molded this to see how it would look like and get an idea of this idea would be feasible. However, we realised this design required too much attaching of different parts of ecoflex ontop of each other, including having our air pocket not being sealed during the layup, making the possibility of air leaks a lot more of a potential issue. As such, we decided to iterate our design.
Design 2
The second design ended up being a lot more like what we had in mind for what we wanted our actuator to look like. Tne mold can be seen in the left, where air chambers were all designed, requiring a smaller seal at the end to fully close off any air gaps. We molded this design, performed the layup, iterated our design to get the best wall thickness for inflation, and eventually tested this design by puncturing the air inlets with a syringe filled with air, to inflate the chambers. This design has 1 set of channels however, so we still needed to iterate our design to make it easier to connect each set of channels to the others.
To complete this iteration of our design, we molded it once more, however, with a slightly different bottom mold for the seal, where a hole dimensioned for a piping was added (slightly smaller than our OD of the tubing as ecoflex is flexible so could mold around the tube), so that we could fit in our pipe to inflate and deflate our design without puncturing it. The videos of our infaltion are shown below
Design 3
From Design 2, we learned a couple of things.
1) The material punctured really easily
2) There was too much outward expansion
3) Three chambers were not necessarily needed, 2 would suffice
4) … it would be nice if we could embed pipes straight into our design
Because of this, I started working on a new design. For this design, I created negative spaces for piping to fit through. I also altered my design so instead of having 3 chambers, I only had 2. The overall concept was that we would be able to make a chain of these modules fit on top of each other, where every other air chamber was offset by 90 degrees, so that we could have individual actuation of the chambers on every other pipe (so that we get more of an esophagus peristalsis motion). This meant I also designed extra spacing for more piping to fit through with negative spaces on my mold, so that our pipe could go throughout the model. You can see this on the right with the individual mold, and the depiction of the molds stacked ontop of each other.
Furthermore, we switched to using a material which was still elastic, however had a larger modulus of elasticity so that it wouldn’t get punctured as easily. When thinking of this in terms of stony coral species, this also proves as an advantage. This material also fixed the issue of the outward expansion, as the making our mold have more material in the outside actually led to it not expanding as easily outwards.
This new material can be seen in the manufactured design in pink.
As we can see in the video on the left, the design deflates on it own, without actually removing the syringe. This occured for 2 reasons, the first as the chambers were connected and I hadn’t closed of the opposite air chamber (the one with the black straw meaning that air was escaping from there). Seconldy, because the pipes actually ended up being a little lose in the mold. This is because of the flexible nature of the mold, even though in therory, creating holes in the CAD for the pipes to give exact hole diameters in the mold was perfect, it actually meant that when the pipes were removed, and added back in, as the material stretches, there is a small air leak around the pipe’s diameter. However, this is easily fixed by brushing on some more silicone material around the pipe.
Design 4
Design 4 was more or less the same as the previous design with 2 core change.
First, I changed my design from having built in poles that created spaces for our pipe to flow through into a hole toleranced for the pipe I had availble to fit in, so that I could get precise hole sizes and build my mold with the pipes designed into it.
Second, I inputted a bridge between the two air cavity chambers. This meant that as I put air into one of the cavities, the other one would get actuated too, hence reducing the number of input places from being 4 to simply 1. This would also mean that I would not need to keep tabs of the pressure in each corresponding chamber as they would inflate and deflate exactly together as they would have the same input and output sources. The results of this can be seen in CAD, and in its design here: